Lichtbogenschweißprozesse bei denen die Schweißstelle mit schützenden Gasen vor Verunreinigungen aus der Luft geschützt werden, nennt man Schutzgasschweißen.
Dabei wird unterschieden zwischen zwei Hauptgruppen unterschieden.
- MSG – Metallschutzgasschweißen (mit abschmelzender Elektrode)
- WSG – Wolframschutzgasschweißen (mit nicht abschmelzender Elektrode)
Einteilung der Schweißprozesse
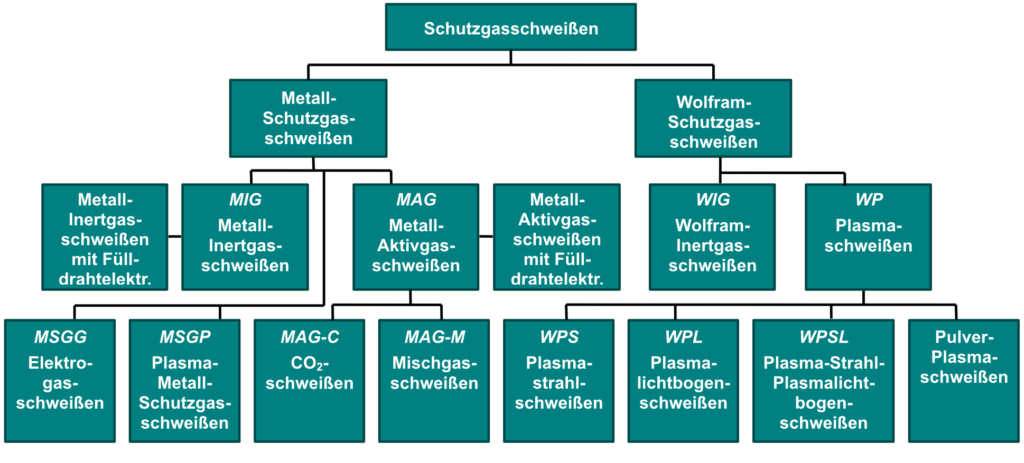
MSG – Metall-Schutzgasschweißen
Ordnungsnummern der Prozesse nach DIN EN ISO 4063
Es folgt einer Auswahl der Ordnungsnummern, die dem MSG zuzuordnen sind.
- 131 – Metall-Inertgasschweißen mit Massivdrahtelektrode
- 135 – Metall-Aktivgasschweißen mit Massivdrahtelektrode
- 136 – Metall-Aktivgasschweißen mit schweißpulvergefüllter Fülldrahtelektrode
- 138 – Metall-Aktivgasschweißen mit metallpulvergefüllter Fülldrahtelektrode
Wärmequelle
Die Wärmequelle beim Schutzgasschweißen ist ein Lichtbogen, welcher zwischen dem kontinuierlich zugeführten Schweißzusatzwerkstoff und den Werkstoffen entsteht. Beim MSG Schweißen wird eine abschmelzende Drahtelektrode verwendet.
Schutzgas
Das Schutzgas schützt dabei die Schweißstelle vor den schädlichen Einflüssen aus der Luft.
- MIG Schweißen von NE-Metallen: Inerte Schutzgase – Argon, Helium oder Mischgase daraus.
- MAG Schweißen von Stahl: aktive Schutzgase – CO2 (MAG-C), Argon-CO2 Gemisch, Argon-Sauerstoff Gemisch und Mehrkomponenten-Gase (MAG-M)
Automatisierung
Das MSG-Schweißen kann teilmechanisch mit von Hand geführtem Brenner, oder vollmechanisiert eingesetzt werden.
Einsatzgebiete
Das MSG-Schweißen kann für nahezu alle Einsatzbereiche eingesetzt werden. Es können sowohl legierte als auch unlegierte Stähle, sowie CrNi-Stähle und Aluminium geschweißt werden.

WSG – Wolfram-Schutzgasschweißen
Ordnungsnummern der Prozesse nach DIN EN ISO 4063
Es folgt einer Auswahl der Ordnungsnummern, die dem MSG zuzuordnen sind.
- 141 – Wolfram-Inertgasschweißen mit Massivstabzusatz
- 142 – Wolfram-Inertgasschweißen ohne Schweißzusatz
- 143 – Wolfram-Inertgasschweißen mit Fülldraht oder Füllstab
- 145 – Wolfram-Inertgasschweißen mit reduzierten Gasanteilen im ansonsten inerten Schutzgas
Auch hier ist die Wärmequelle ein Lichtbogen, aber im Gegensatz zum MSG entsteht diese hier zwischen einer nicht abschmelzenden Wolframelektrode und dem Werkstück. Als inerte Schutzgase werden Argon, Helium oder Gemische daraus verwendet. Für manche Werkstoffe werden auch Argon-Wasserstoff Gemische verwendet.
Auch Wolfram kann nicht unbegrenzt thermisch belastet werden. Dies wirkt sich sowohl auf die Abschmelzleistung, als auch auf die Schweißgeschwindigkeit aus.
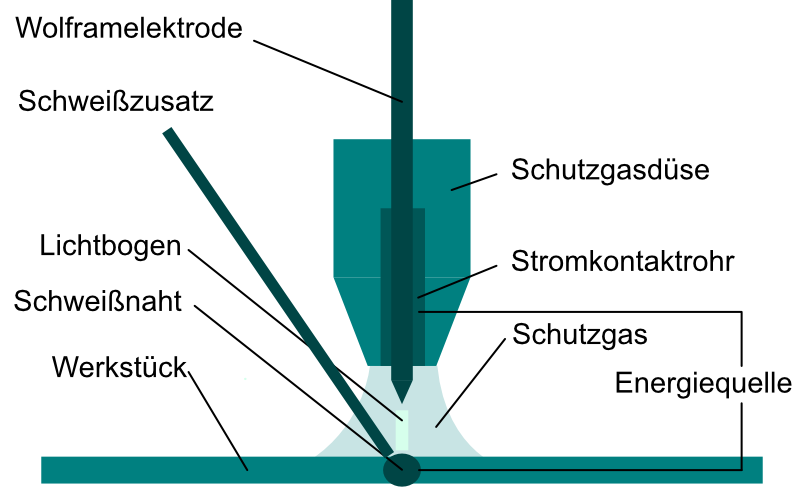
WIG – Wolfram Inertgasschweißen
Eine Schweißanlage zum WIG Schweißen besteht aus folgenden Komponenten
- Schutzgasversorgung (z.B. Gasflasche mit Schutzgasschlauch zur Schweißstromquelle)
- Schweißstromquelle mit Steuer- und Zündgerät (mit Netzanschluss)
- Schlauchpaket (Strom, Gas, Wasser)
- Schweißbrenner
- Schweißstromrückführung (Erdung)
- Zusatzwerkstoff
- Werkstück
Positionen, Wirtschaftlichkeit
Mit WIG können NE-Metalle und Stähle in allen Positionen verschweißt werden. Wobei fallende Nähte schwierig bis gar nicht möglich sind. Wirtschaftlich ist WIG-Schweißen üblicherweise im Blechdickenbereich 0,5 – 5 mm.
Brenner
Der Brenner variiert je nach geforderter Leistung. Es werden entweder gas- oder wassergekühlte Brenner verwendet. Gasgekühlte Brenner werden bei bis zu 250 Ampere eingesetzt. Liegst die Stromstärke darüber oder ist eine hohe Einschaltdauer von Nöten, werden wassergekühlte Brenner benutzt.
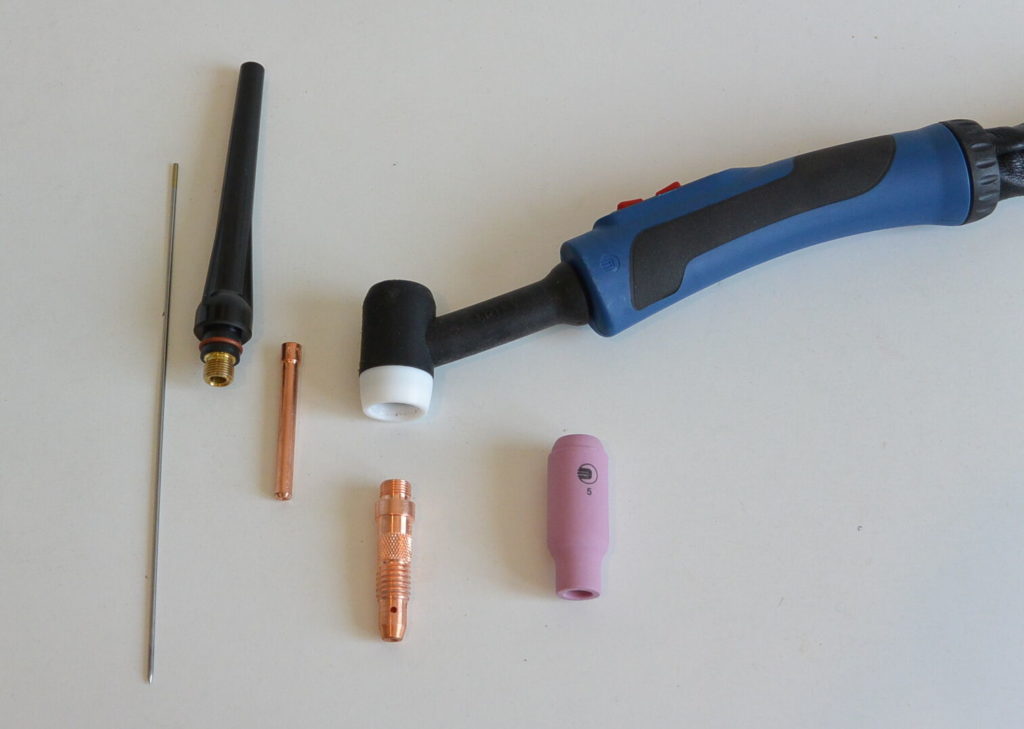
Von links nach rechts
- Wolframelektrode
- Brennerkappe
- Spannhülse
- Spannhülsengehäuse
- Handstück
- Gasdüse
Wolframelektroden
Die Wolframelektrode ist maßgeblich für die Qualität der Schweißnaht verantwortlich. Es wird hierbei zwischen reinen Wolframelektroden und welchen mit Oxidzusatz unterschieden. Welcher Durchmesser bei welcher Stromart mit oder ohne Oxidzusatz verwendet wird, kann aus der DIN EN ISO 6848 entnommen werden.
Außerdem ist es ebenso wichtig, dass die Elektrode am Ende die richtige Form aufweist. Dies hängt ebenso von der Stromquelle und Stromstärke ab.
Die Werkstoffzusammensetzung von Wolframelektroden lässt sich anhand einer farbigen Kennzeichnung nach DIN EN ISO 6848 ablesen.
Schutzgase
Das Schutzgas ist maßgeblich für die Form des Lichtbogens bzw. die Einbrandtiefe verantwortlich. Das Schutzgas wird vor dem Zünden des Lichtbogens unter Berücksichtigung einer gewissen Vorströmzeit geöffnet. Dies gewährleistet ein Verdrängen der Luft um die Naht herum.
Zünden des Lichtbogens
Der Lichtbogen kann beim WIG Schweißen entweder kontaktlos oder mit Kontakt zum Werkstück gezündet werden. Beim kontaktlosen Zünden wird das Einbringen von Wolfram in die Naht vermieden. Die Ionisation (Erzeugung von Ladungsträgern) des Lichtbogenraumes wird durch hochfrequente Hochspannungsimpulse (max. 12 kV / 20 kV bei mechanisch geführten Brennern) erreicht. Durch die Ionisation wird das Gas leitend und der Lichtbogen kann kontaktlos gezündet werden. In der Umgebung der WIG Anlage müssen dabei alle elektrischen Geräte gegen störende Strahlung geschützt sein. Die WIG Anlage muss dabei insbesondere an den Stellen, zu denen der Mensch Kontakt haben kann, gut isoliert sein.
Das Zünden des Lichtbogens kann auch durch einen Kurzschluss (Lift-Arc Zündung) erfolgen. Dabei wird die Elektrode kurz mit dem Werkstück in Kontakt gebracht.
Nach dem Zünden des Lichtbogens fließt dann der eingestellte Schweißstrom.
Formieren
Beim Schweißen von hochlegierten Stählen wird meistens formiert. Dabei wird der Bereich an der Schweißnahtwurzel mit Schutzgas geflutet. Bei kleinen Bauteilen wird das Ganze Bauteil abgedichtet und mit Gas geflutet. Bei großen Bauteilen werden dazu sogenannte Formierkammern eingesetzt. Durch das Formieren wird die Schweißnahtwurzel vor den schädlichen Einflüssen der Luft geschützt. Dadurch wird Oxidation (Anlaufen) vermieden. Sind die Nähte angelaufen, können diese durch mechanischen oder chemischen Abtrag wieder entfernt (schleifen, beizen etc.) siehe dazu auch MB 826 der Informationsstelle Edelstahl Rostfrei.
Formiergas | Werkstoffe |
Argon-Wasserstoff Gemische |
|
Stickstoff-Wasserstoff Gemische |
|
Argon |
|
Stickstoff |
|
Mechanisierung
WIG Schweißen kann wie folgt mechanisiert werden:
- von Hand
- teilmechanisch
- vollmechanisch
- automatisch
WIG Verfahren
- WIG Impulsschweißen
- WIG Schweißen mit Zusatzdraht
- WIG Schweißen mit Kaltdraht
- WIG Schweißen mit drehbarem Bauteil
- WIG Orbitalschweißen
- WIG Orbital-Engspaltschweißen
- WIG Heißdrahtschweißen
- WIG Mehrkathodenschweißen
- WIG Schweißen mit einer Doppelgasdüse
- WIG Punktschweißen
- WIG Schweißen mit zwei Brennern gleichzeitig (Stereo)
- WIG Stichlochschweißen
MSGP – Plasma-Metall-Schutzgasschweißen
Bei dem Verfahren handelt es sich um eine Mischung aus dem Metallschutzgasschweißen und Plasmaschweißen. Am Anfang der Naht schmilzt der Lichtbogen den Werkstoff auf, bevor die Drahtelektrode aufgeschmolzen wird. Die Plasmastromquelle mit steil fallender Kennlinie und die MSG Schweißstromquelle mit steil fallender, oder flach fallender Kennlinie kommen bei diesem Verfahren zum Einsatz.
WP – Wolfram-Plasmaschweißen
Beim Wolfram-Plasmaschweißen brennt der Lichtbogen entweder zwischen der Wolframelektrode und einer Wassergekühlten Kupferdüse (WPS) oder dem Werkstück (WPL). Der Lichtbogen brennt in einer Inertgas Atmosphäre. Die Kupferdüse schnürt den Lichtbogen ein und erlaubt so eine höhere Leistungsdichte.
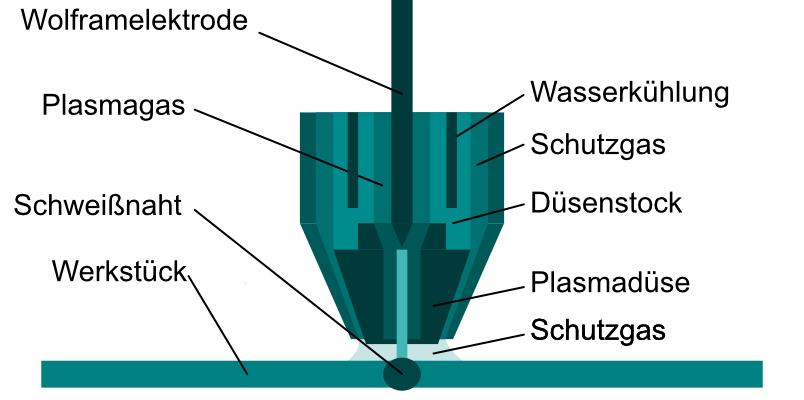
Schutzgase
Die Schutzgase schützen sowohl den Zusatzwerkstoff, die Elektrode als auch das Schmelzbad vor schädlichen Einflüssen der Luft. Stick- und Sauerstoffeinschlüsse in der Naht würden diese spröde machen.
aktive Gase
aktive Gase rufen chemische oder physikalische Reaktionen im Lichtbogen aus.
inerte Gase
inerte Gase führen zu keinen chemischen Reaktionen beim Schweißen.
Unterscheidung nach Anforderung
- Reaktionsverhalten (inert, oxidierend, reaktionsträge, reduzierend)
- Dichte (leichter oder schwerer als Sauerstoff)
- Wärmeleitfähigkeit
- Ionisations- Dissoziationsenergie (Lichtbogenkennlinie)
- Siedetemperatur
Eigenschaften
Welche Schutzgase mit welcher Werkstoffgruppe geschweißt werden können wird in der DIN EN ISO 14175 genormt.
Gas | Chemisches Zeichen | Spezifische Eigenschaften bei 0 °C und 1013 hPa | Reaktionsverhalten | ||
Dichte [kg/m³] | relative Dichte zu Luft [1,293 kg / m³] | Siedetemperatur [°C] | |||
Argon | Ar | 1,7484 | 1,380 | -185,9 | inert |
Helium | He | 0,138 | 0,138 | -268,9 | inert |
Kohlendioxid | CO2 | 1,977 | 1,529 | -75,5a) | oxidierend |
Sauerstoff | O2 | 1,429 | 1,105 | -183,0 | oxidierend |
Stickstoff | N2 | 1,251 | 0,968 | -195,8 | reaktionsträgeb) |
Wasserstoff | H2 | 0,009 | 0,070 | -252,8 | reduzierend |
a) Sublimationstemperatur (Übergangstemperatur vom festen in den gasförmigen Zustand).
b) Das Verhalten von Stickstoff verändert sich je nach Werkstoff und Anwendungsfall. Mögliche Einflüsse können negativ sein und müssen beachtet werden.
Die benötigte Schutzgasmenge und die Dichte stehen in Abhängigkeit vom Heliumanteil im Argon.
Gas / Gasgemisch | Dichte [kg/m³] | Korrekturfaktor (Multiplikator) |
100% Ar | 1,78 | 1,00 |
75% Ar 25% He | 1,29 | 1,14 |
50% Ar 50% He | 0,92 | 1,35 |
25% Ar 75% He | 0,54 | 1,75 |
100% He | 0,17 | 3,16 |
Wärmeleitfähigkeit von Schutzgasen und Zumischkomponenten
Die Wärmeleitfähigkeit hat Einfluss aus:
- Nahtformung
- Schweißbadtemperatur
- Schweißbadentgasung
- Schweißgeschwindigkeit
Einteilung von Schutz- und Prozessgasen
Auch diese Einteilung findet in der DIN EN ISO 14175 statt.
Hauptgruppe
Symbol | Komponenten in Volumen % (nominell) | ||||||
Hauptgruppe | Untergruppe | oxidierend | inert | reduzierend | reaktionsträge | ||
CO2 | O2 | Ar | He | H2 | N2 | ||
I | 1 | 100 | |||||
2 | 100 | ||||||
3 | Rest | 0,5 ≤ He ≤ 95 | |||||
M1 | 1 | 0,5 ≤ CO2 ≤ 5 | Resta | 0,5 ≤ H2 ≤ 5 | |||
2 | 0,5 ≤ CO2 ≤ 5 | Resta | |||||
3 | 0,5 ≤ O2 ≤ 3 | Resta | |||||
4 | 0,5 ≤ CO2 ≤ 5 | 0,5 ≤ O2 ≤ 3 | Resta | ||||
M2 | 0 | 5 ≤ CO2 ≤ 15 | Resta | ||||
1 | 5 ≤ CO2 ≤ 25 | Resta | |||||
2 | 3 ≤ O2 ≤ 10 | Resta | |||||
3 | 0,5 ≤ CO2 ≤ 5 | 3 ≤ O2 ≤ 10 | Resta | ||||
4 | 5 ≤ CO2 ≤ 15 | 0,5 ≤ O2 ≤ 3 | Resta | ||||
5 | 5 ≤ CO2 ≤ 15 | 3 ≤ O2 ≤ 10 | Resta | ||||
6 | 15 ≤ CO2 ≤ 25 | 0,5 ≤ O2 ≤ 3 | Resta | ||||
7 | 15 ≤ CO2 ≤ 25 | 3 ≤ O2 ≤ 10 | Resta | ||||
M3 | 1 | 25 ≤ CO2 ≤ 50 | Resta | ||||
2 | 10 ≤ O2 ≤ 15 | Resta | |||||
3 | 25 ≤ CO2 ≤ 50 | 2 ≤ O2 ≤ 10 | Resta | ||||
4 | 5 ≤ CO2 ≤ 25 | 10 ≤ O2 ≤ 15 | Resta | ||||
5 | 25 ≤ CO2 ≤ 50 | 10 ≤ O2 ≤ 15 | Resta | ||||
C | 1 | 100 | |||||
2 | Rest | 0,5 ≤ O2 ≤ 30 | |||||
R | 1 | Resta | 0,5 ≤ H2 ≤ 15 | ||||
2 | Resta | 15 ≤ H2 ≤ 50 | |||||
N | 1 | 100 | |||||
2 | Resta | 0,5 ≤ N2 ≤ 5 | |||||
3 | Resta | 5 ≤ N2 ≤ 50 | |||||
4 | Resta | 0,5 ≤ H2 ≤ 10 | 0,5 ≤ N2 ≤ 5 | ||||
5 | 0,5 ≤ H2 ≤ 50 | Rest | |||||
O | 1 | 100 | |||||
Z | Mischgase mit Komponenten, die nicht in der Tabelle aufgeführt sind oder Mischgase mit einer Zusammensetzung außerhalb der angegebenen Bereiche.b |
a) Für diese Einteilung darf Argon teilweise oder vollständig durch Helium ersetzt werden.
b) Zwei Mischgase mit derselben Z-Einteilung dürfen nicht gegeneinander ausgetauscht werden.